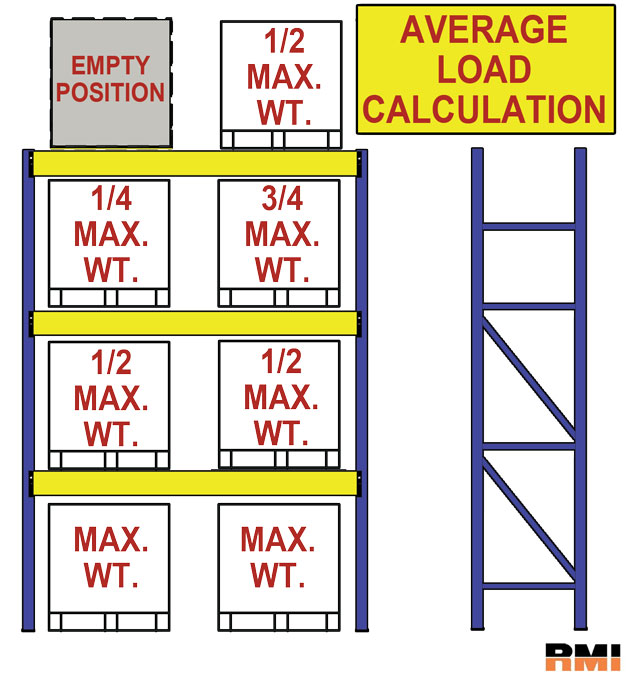
The revised American National Standard for storage rack, ANSI MH16-1-2021, was recently published by the Rack Manufacturers Institute (RMI), and includes new requirements for calculating the load capacity for a pallet rack application. The previous standard, published in 2012, calculated capacities using only the column unbraced length. New guidance in the 2021 revision uses several additional factors that affect the stiffness of the pallet rack structure to calculate the capacity.
The capacity of the frame will depend on nine factors beyond just the length of the unbraced column span, including:
- Average load to maximum load ratio
- Beam-to-column connector stiffness and strength
- Beam stiffness
- Column stiffness
- Base plate and anchorage detail
- Site seismicity
- Number of storage levels
- Aspect ratio of the frame, or height-to-depth ratio
- Warehouse or Retail environment
In order to determine if the global stiffness of the rack assembly meets the new requirements, the designer will need to perform several calculations using the above nine criteria. Rack users need to understand that a frame capacity calculated in accordance with the 2021 standard may be less than the capacity calculated using the 2012 standard, all things being equal.
Users should be careful using traditional upright capacity tables because there are so many other factors to consider now. Tables can be used as an initial guide, but more calculations must be completed before a frame capacity is accurate and final. With a reasonable average load assumption and stiffer connectors at lower beam levels, in most cases the rack design will be similar to capacities calculated under 2012 standard. In some cases, no rack design changes will be needed.
One important, key factor to determining a capacity with a greater chance of correlation to the 2012 standards is the AVERAGE LOAD DATA. If the average load data at the facility is available, and connectors with adequate stiffness are selected, then the calculated frame capacity may be close to the capacity calculated under the 2012 requirements. In such cases, the average load data provided will become part of the design assumption and must appear on the load application and rack configuration (LARC) drawings and the load plaques.
*** Please note that the RMI does not allow a load that is less than 67% of the maximum load for the calculation. ***
While the new methods make frame selection a bit more complex, there are also advantages. One such advantage can come from identification of an average product load per bay, as opposed to a traditional maximum product loading calculation. Many storage racks utilize an average loading that is less than the maximum loading in all storage locations. This may be due to empty positions with no load, or the number of bays with lighter product pallets. Failure to identify an average product load will likely require the use of stiffer connections or an increase in the column strength to comply with the 2021 revision requirements compared to the 2012 requirements.
More information will definitely be needed to determine a calculated capacity and this will cause users to get more involved in the design. Once consumers start looking at the nine factors listed above, they will be more educated for future projects and start looking for average load data, so they are not forced to use the higher criteria, which will usually come with a higher price tag.
The consideration of all of the above factors makes working with the rack designer even more important than ever. With a thorough understanding of your rack application, a rack designer will be able to select the most economical frame that still complies with the 2021 standard. UNARCO Engineers can help navigate the new code and help with an economical design to increase efficiency in any warehouse or distribution center.